CASE STUDY
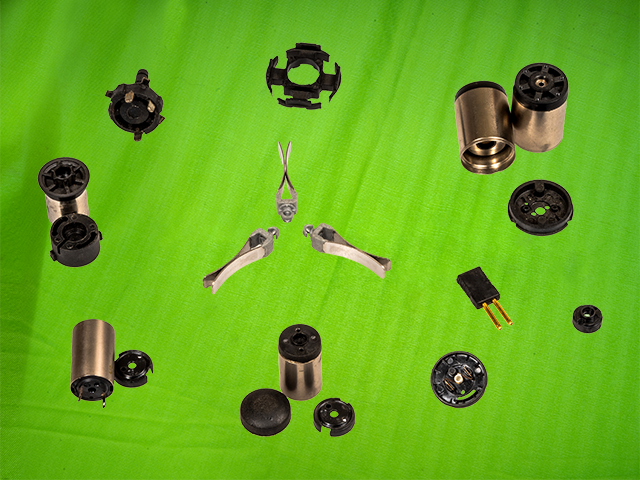
The EOU unit from Seepz Mumbai was searching for a suitable molder who had the tooling and molding capabilities to produce micro-injection parts for servo motor components that required over-molding. PPS65%GF (Fortron) was suggested due to its ability to withstand the continuous running conditions of a servo motor. The job involved over-molding two small metal parts, an SS304 sleeve and a magnet, with a required concentricity accuracy of 30 microns. Despite the critical nature of the job, we were able to simplify the process with our expertise in tool design and molding capabilities, using conventional molding techniques. As a result, we were able to develop 10-12 different components for them.
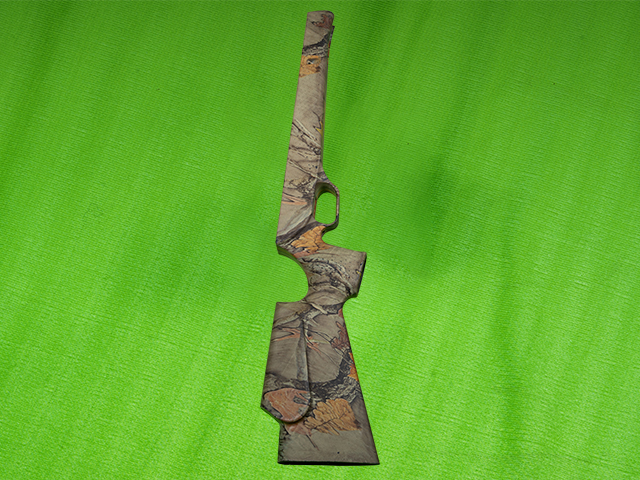
Converting a rifle butt from wood to plastic- A typical challenge that supports initiatives such as “Save Earth-Save Trees”. Preciholes reached out to us to see the feasibility of converting their wooden butt to plastic, which was made easily using PA630%GF material. The design was made in such a way that a single butt could serve the purpose for both right-handed and left-handed users. Preciholes informed us that there was a universal practice to use separate butt designs, as ambidextrous users are uncommon. Development is ongoing to produce the entire body of revolvers, guns, and rifles in plastic.
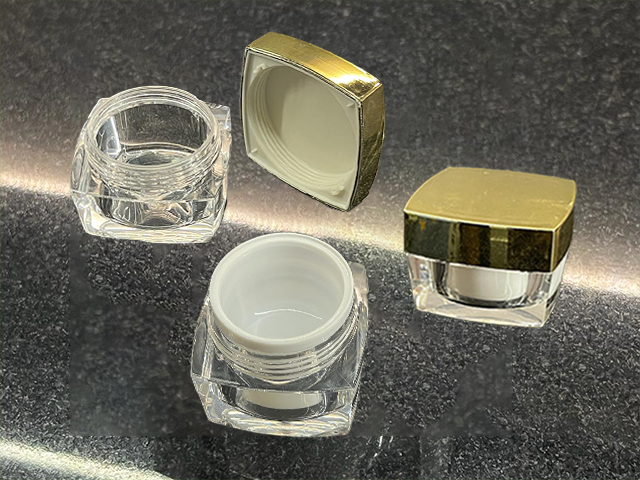
After seeing thin molding produced with conventional machines, do you think a thick skin would be a challenge for us? Take a look at this acrylic crème container. The FMCG supplier had ambitious plans for a lucrative container shape with a glossy surface. The threads also needed to match up with the square-shaped shoulder of the cap, and we achieved this through precise control while machining the tool. As a Poka-yoke measure, a sensor was set to ensure the ZERO position of the thread during the unscrewing mechanism of the mold and the core-in sequence in the next cycle. We were able to produce over 12mm wall thickness in acrylic at a rate of 500ppm.